Transformative Transformer Teamwork
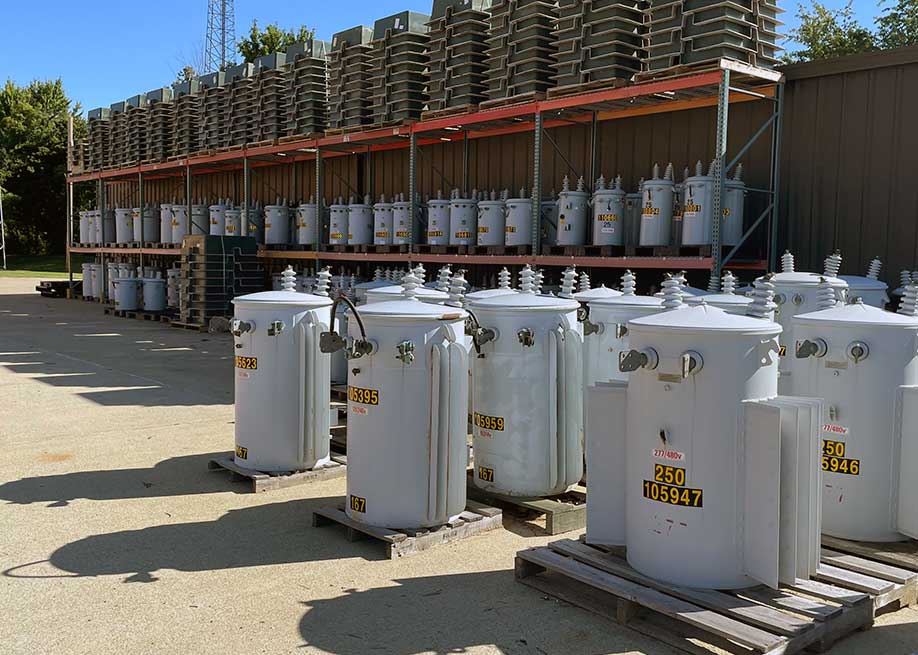
As Holland develops and grows, essential pieces of infrastructure such as electric distribution equipment must also grow and develop to support our community. To support this growth and to position our community for future success, it’s critically important to keep a supply of transformers and other infrastructure materials on hand.
Most of us began to notice supply chain shortages in the early stages of the pandemic when we had trouble finding toilet paper at the grocery store.
For Holland BPW, the pinch came about a year later, when orders for transformers and other electric distribution equipment that typically had a lead time of four weeks suddenly had an estimated lead time of two to three years as these steel components faced shipping delays from the pandemic and the war in Ukraine.
Purchasing
To keep this equipment in stock and ready for the electric distribution team, the purchasing team had to get creative. All Holland BPW vendors must meet high standards for excellence in order to keep our services reliable, and the purchasing department searched for new potential vendors to avoid product shortages with our previously approved vendors.
In the search process, the purchasing team found a new transformer manufacturer with shorter lead times that met engineering’s needs and quality requirements in a more reasonable timeframe.
All Hands on Deck
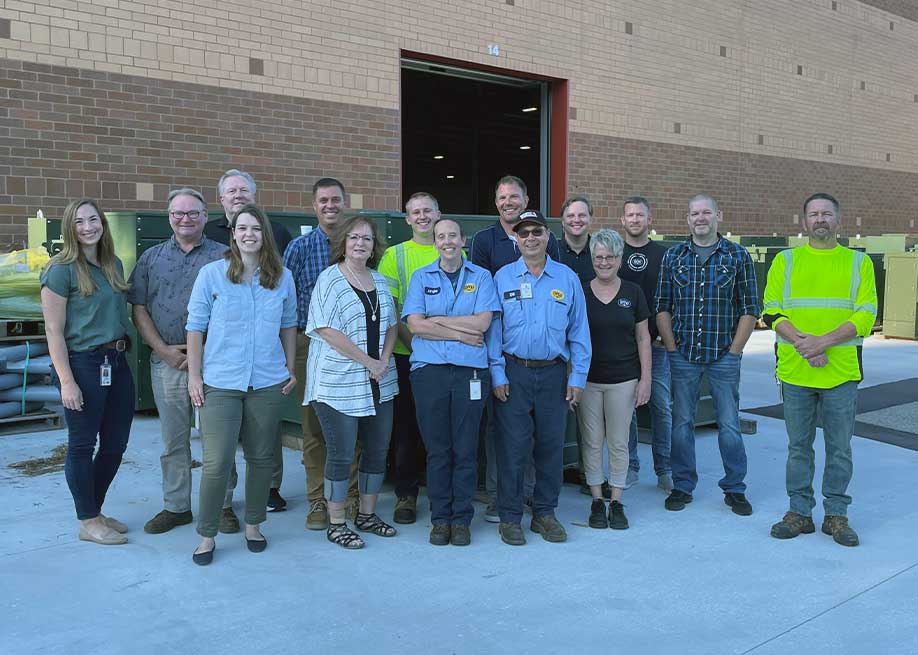
While BPW policy encourages our teams to seek the lowest cost option, our warehouse and purchasing teams worked together closely to compare costs to lead times and make the best choice in order to keep essential items like transformers and metering equipment on storage shelves.
Likewise, the engineering group collaborated with these teams to approve new manufacturers in order to bypass long supply chain delays and allow our teams more flexibility. Finding just-right replacements required collaboration to not only find the best product, but to also think through how these alternatives might change processes, installation, required tools or safety procedures needed to get the job done right. Every team member put in more hours in order to vet, approve, ask for quotes and make the best decisions for HBPW customers.
In order to make room for all of the items needed, the warehouse and facilities teams also added new racking and expanded outdoor storage space at the Service Center to make the most of our physical space. They even removed grass in outside staging areas to pour new concrete that could store the heaviest equipment and transformers outdoors, making room for other materials in the warehouse.
Mutual Aid
As a community-owned utility, Holland BPW participates in a variety of public power organizations, including the American Public Power Association’s (APPA) network of Mutual Aid participants. Mutual Aid provides standard agreements between other publicly-owned utilities to share resources in times of crisis such as major storms, tornados or hurricanes to turn the power back on in a reasonable, safe time frame.
In May, APPA recognized the critical need that many of their utility members faced concerning supply chain delays for transformers and set their Mutual Aid Network in motion. The same network used to keep the power reliable for areas in crisis mobilized to offer voluntary transformer exchanges so that utilities in need could more easily share resources without sacrificing any essential services to customers.
Thankfully, because of our teams’ creativity, Holland BPW did not have to ask for additional transformers from other utilities, and even offered a limited number of transformers determined to be above our surplus for other local power providers who were in dire need.
Most of all, we’re thankful for the HBPW teams who made resourceful solutions like this possible. The collaboration required to provide excellent, essential services to our customers is impressive, and we don’t take that for granted.